Rings are an intimate form of jewellery. Unlike a pendant or earring, there is nothing one-size-fits all about something that must sit snugly on a finger. Balancing the demands of beauty, comfort and utility, even the simplest design involves great intricacy.
“I still really love making rings,” says Sam Sherry, a master craftsman and workshop manager at Graff. “They’re such a condensed piece of jewellery.” Sherry began at the British jewellers eighteen years ago as a ring mounter. Over nearly two decades, he’s watched the world of jewellery craftsmanship transform as millennia-old techniques are supplemented with the wonders of digital imaging and printing.
The journey starts with the stone. What we call a ‘single stone ring’ is often set with smaller shoulder stones, such as tapered baguettes or pears. When these arrive in the workshop, they are unboxed and scanned.
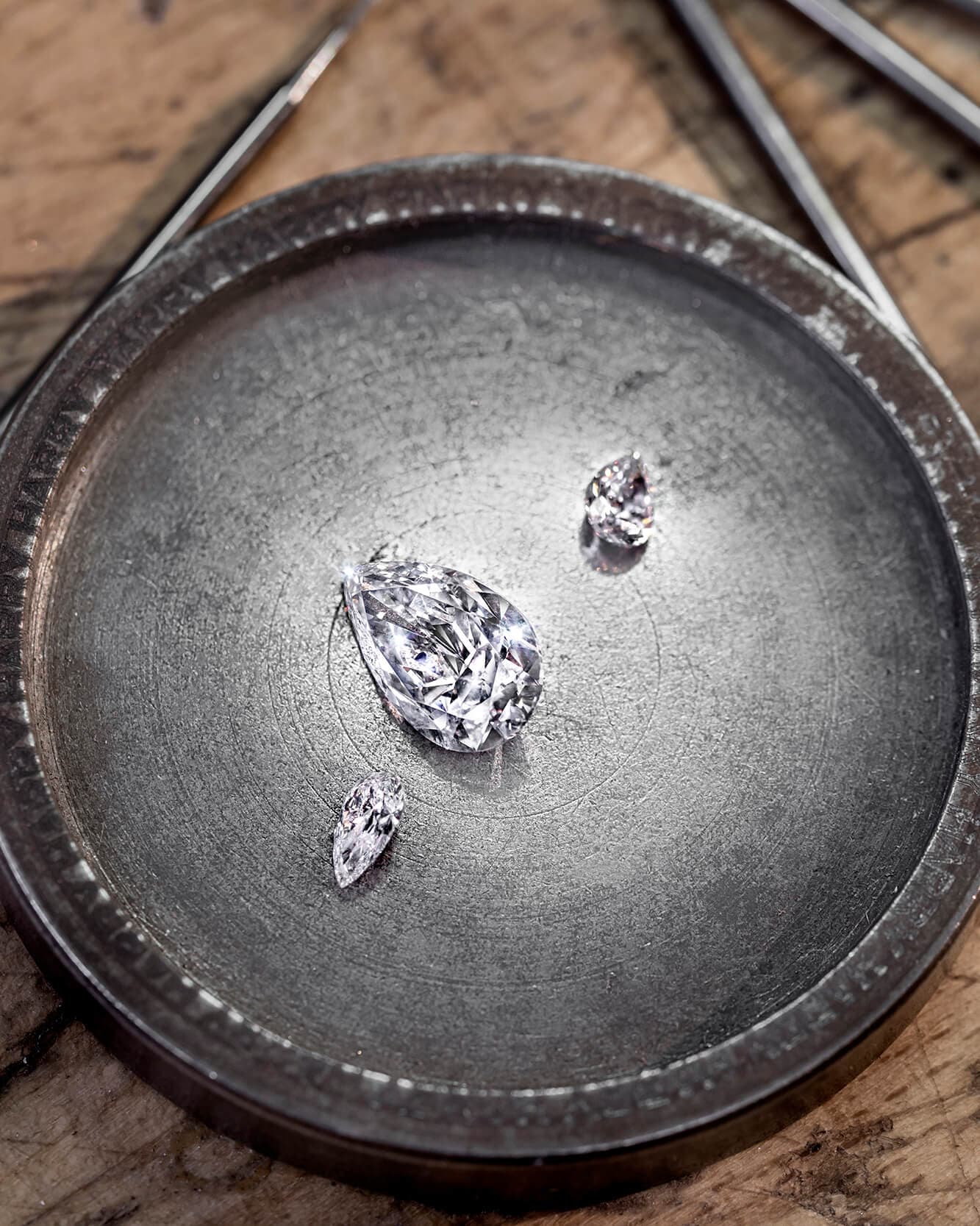
“We instantly capture every facet of those stones so that we can more accurately build an elegant mount,” Sherry explains. Scanning not only allows a greater degree of visualisation when it comes to height, weight, and placement of each gem, but eliminates surprises.
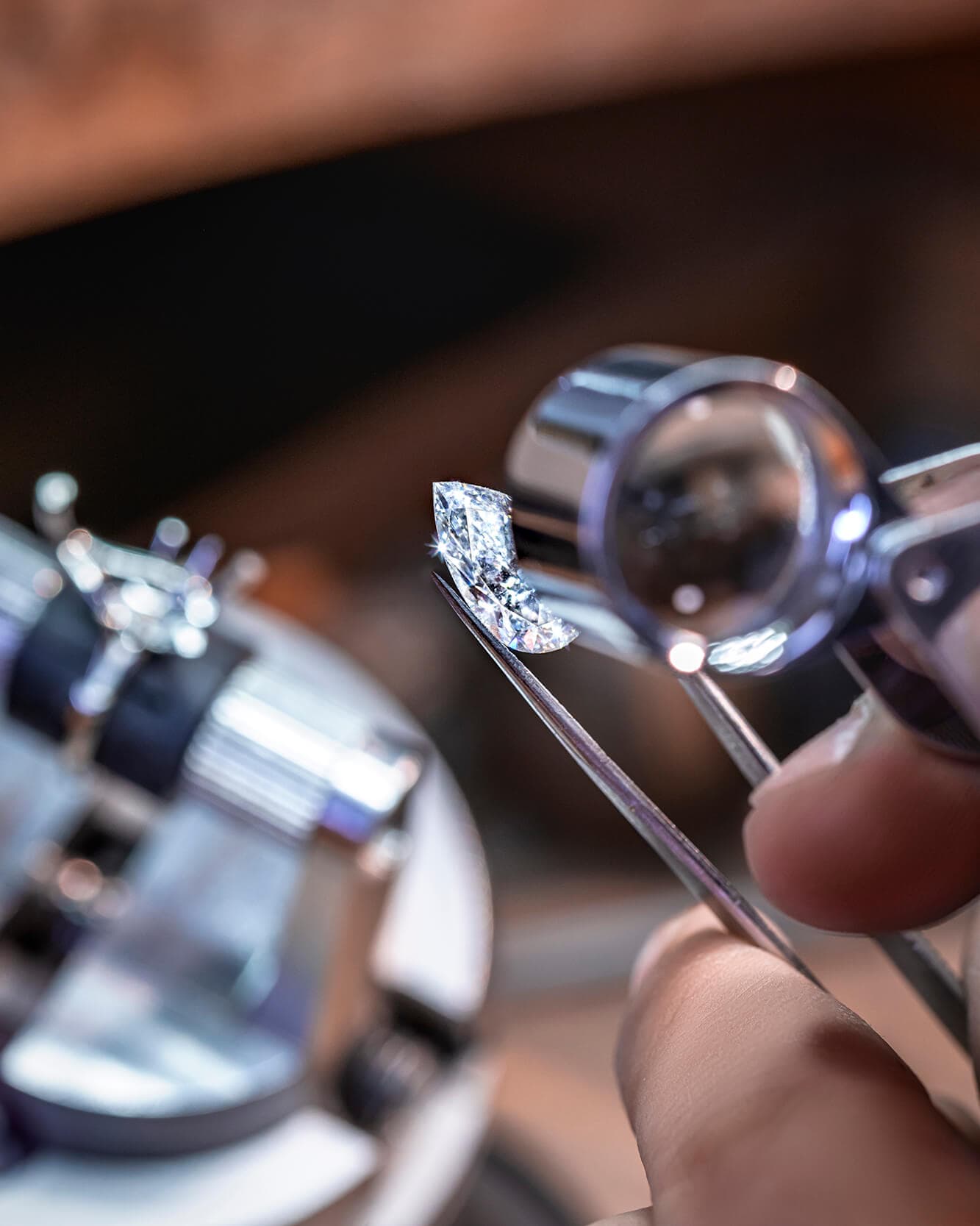
The craft process is intended to maximise the properties of a stone: the sparkle of a white diamond, the saturation of a yellow diamond. But there can be unforeseen challenges. “Sometimes with a sapphire or a ruby, from above you'll have this beautiful homogenous colour, this deep hue,” says Sherry. “But if you look at the stone from the side, the culet might be severely over to one side. That's where all the colour is.” The culet is the point where the facets meet on the belly of a stone. Perfect symmetry and distribution of colour is easier to achieve if you can foresee such issues and accommodate them in the initial mount design.
Rings undergo several stages of visualisation and prototyping before being made. The component parts are 3D-printed using a wax-based photopolymer resin, ready for casting. Lost wax casting is an ancient process in which clay moulds are formed around wax models before being fired. The wax melts away, leaving a negative space for molten metal – in this case platinum or 18 carat gold – to be poured into. The traditionally used clay has now been updated to a precision investment powder to improve the quality of the resulting precious metal casting. The ring then goes into the workshop, where “everything is adjusted, prepared and finalised by hand.” There it will be assembled, hallmarked, set, adjusted, finished, and repeatedly polished.






Each of these stages is carefully handled by the artisan’s ateliers, marrying their expert eye and intuitive knowledge with age-old techniques. Their tools are many and varied: moulds, files, emery papers, pliers, tweezers, solders, lasers, cotton threads charged with polishing compound. It is both art and science. Bespoke pieces can go through “an almost infinite number of stages” of refining and modifying, but the attentiveness to line, light and wearability remains the same across the design spectrum. It’s an extraordinarily time-intensive process, often focused on minutiae that might seem invisible to the naked eye but transforms how the piece is seen and worn. “The beauty of these rings is in a 10th of a millimetre,” notes Sherry.
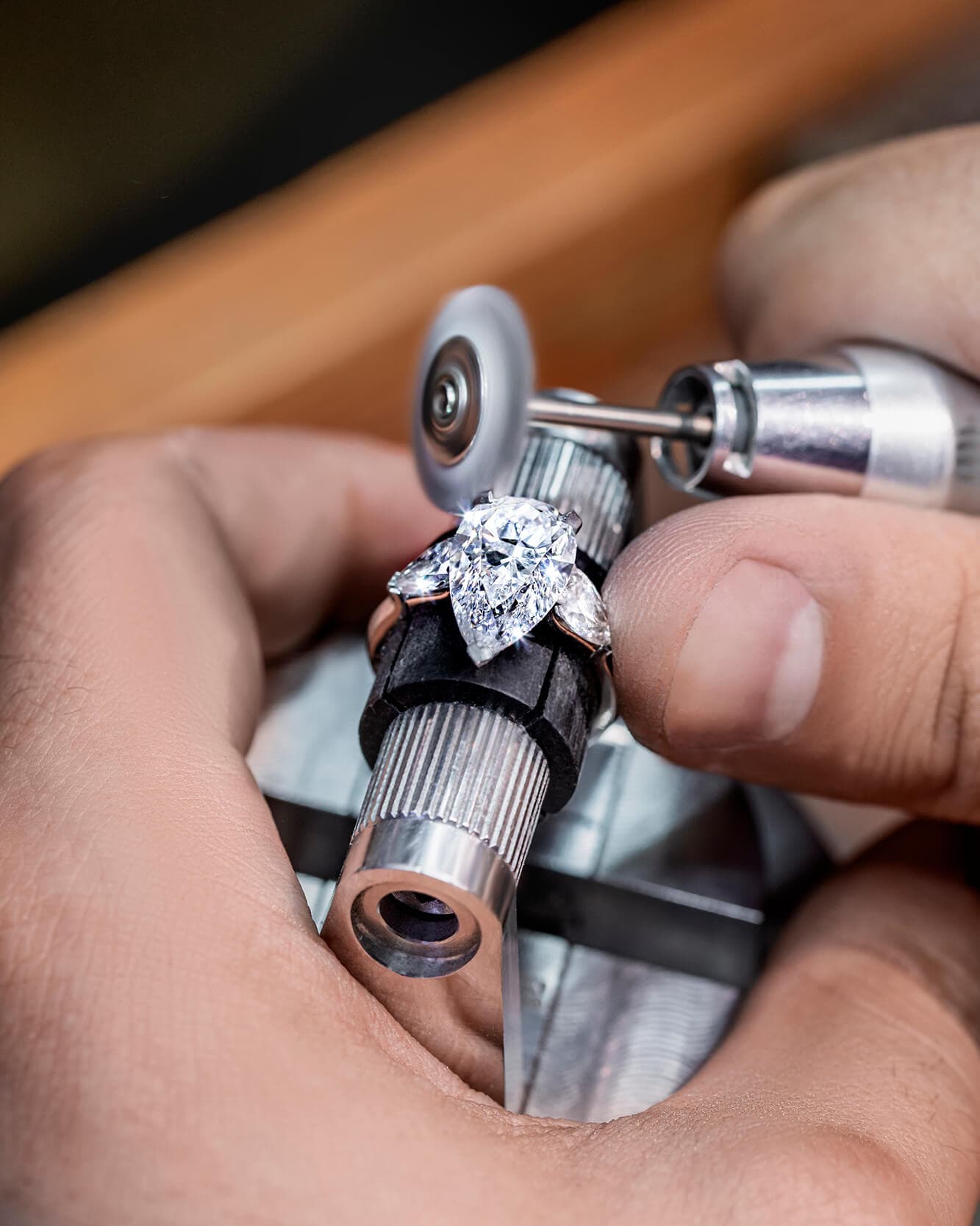
Such technical abilities can take decades to perfect. “To become a true master craftsman, you're probably looking at fifteen to twenty years to be truly capable,” Sherry says. “It really does have to be a dedication… more of a vocation than a job.”
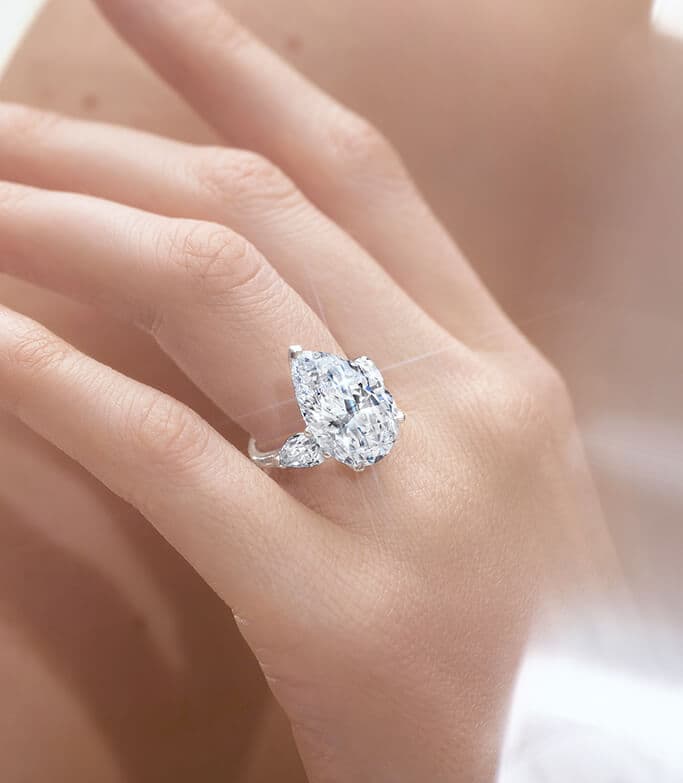
With everything made in-house at Graff, collaboration is also vital. A setter can go next door to talk to a mounter. A designer can head downstairs and see the piece in progress. The final product is an accumulation of hours of work, years of learning, and a combination of centuries-old techniques and rapidly developing technologies. Ideally, these rings will survive for centuries more.
“Hopefully they’ll become heirlooms,” says Sherry. “We make our rings in such a way that they [can]… be worn by future generations.”